ORIGINAL SYSTEM
生産計画から納品までのすべてを支える、
最新鋭の自社オリジナルシステム
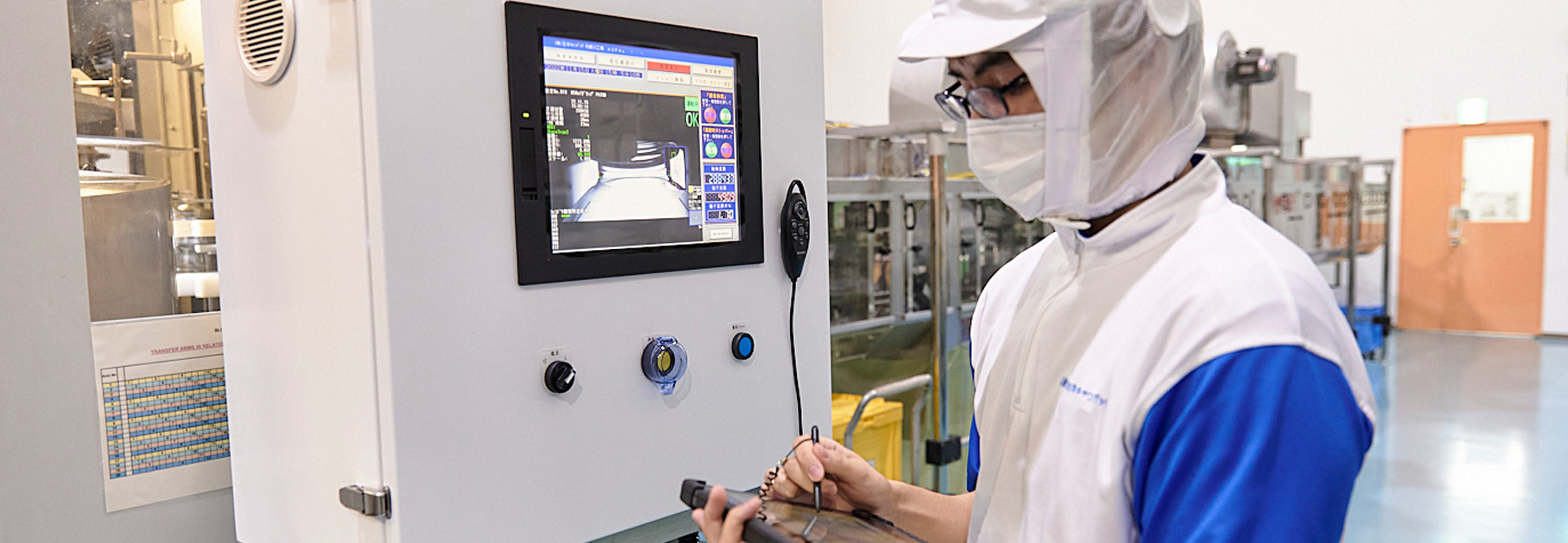
「生産・調達・物流情報共有化システム(通称「PSPシステム」)」は、ほぼすべての部署に導入されており、業務において日々活用されています。
円滑かつ正確な仕事を実現するだけでなく、
常に改善・改良を重ねることで、競争力の強化につながるワークフローとサプライチェーンを構築しています。
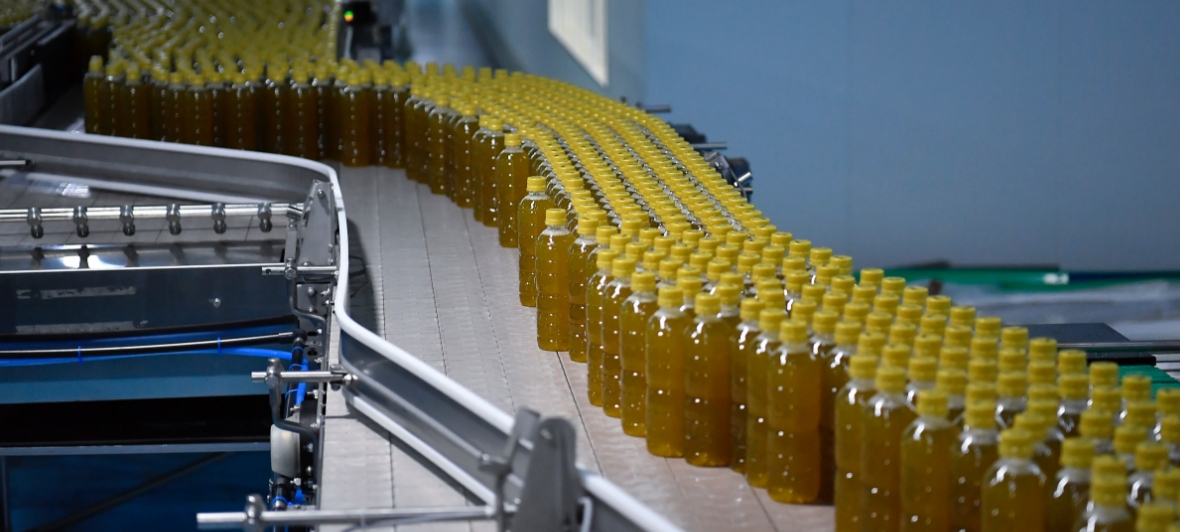
お客様、協力会社様、
現場の従業員。
全関係者に最適なシステムを
-
お客様との
情報共有化 -
製品
トレーサビリティ
情報の
共有化
-
生産情報の
共有化
システム作りにおいてもっとも重視したのは、効率的かつ正確な情報の共有です。〈お客様との情報共有化〉〈製品トレーサビリティ情報の共有化〉〈生産情報の共有化〉を目的としました。
しかし、その作業は決して簡単ではありません。
まず現状の工程と出来高の把握から始まり、業務そのものの見直し、また関係者のITシステムに対する苦手意識の払拭など、乗り越えるべき課題はたくさんあります。
それらすべてに対応するために、「現場作業の効率を徹底的に分析する」「情報収集を簡単に」「運用が始まってからも、システム変更が容易にできるように」「新しい情報共有コストを削減する」「情報共有コスト増加を抑える」といった指針を掲げながら、開発作業が進められていきました。
導入により、コストと
時間の大幅な削減が実現。
徹底したトレーサビリティも
そして出来上がったのが、「生産・調達・物流情報共有化システム(Pio
Supply chain Planning system=PSPシステム)」です。
PSPシステムの導入により、発注をいただくと生産計画がシームレスに連動し、それまで3営業日程度かかっていた1ヶ月分の生産計画の作成が、半日でできるようになりました。また専門性も必要なく担当であれば誰もが作成できる、情報共有がボタンひとつで即時にできるといったメリットもあり、PSPシステム中心の作業工程が確立されました。
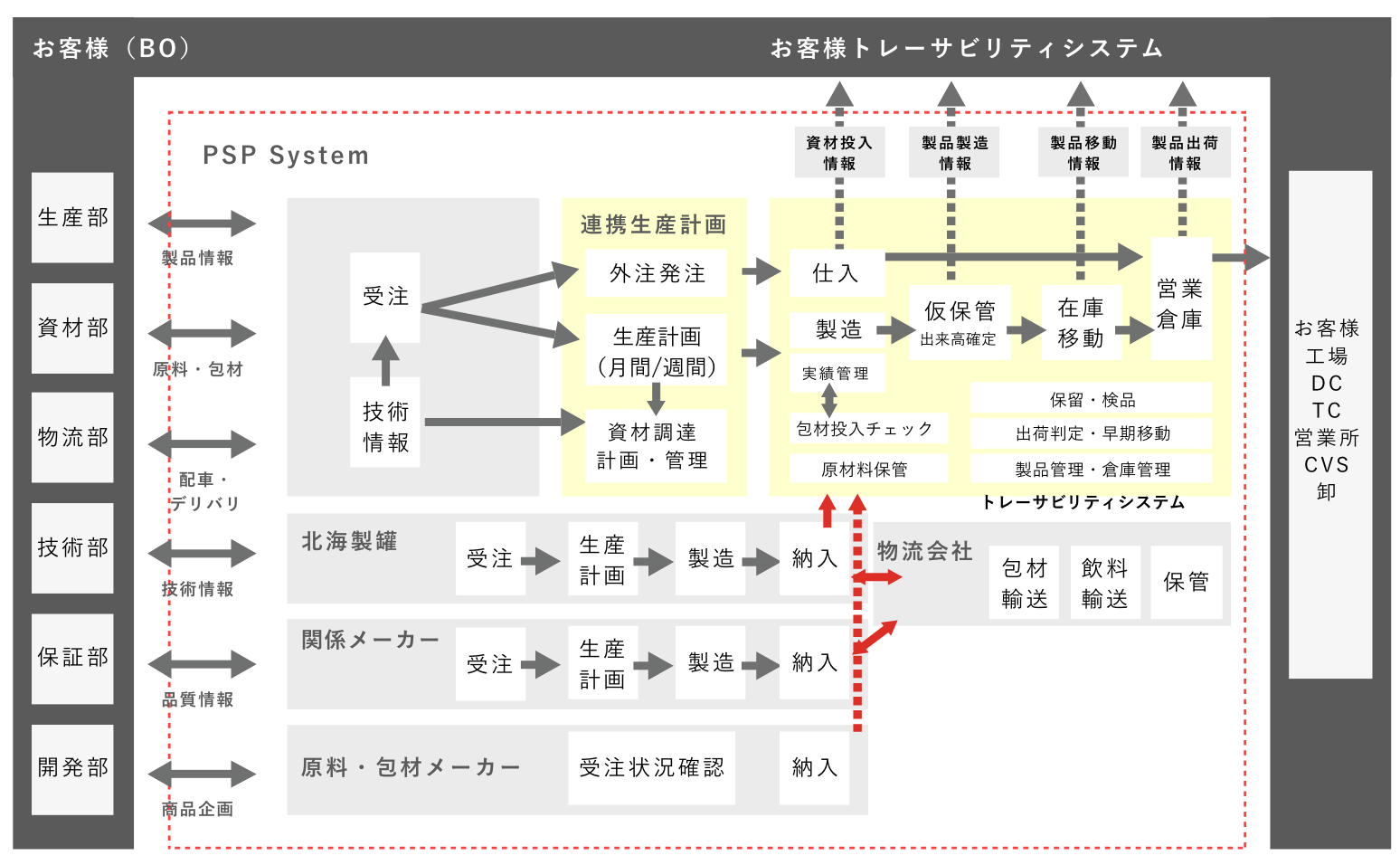
さらには、資材がいつどのくらい必要なのか、
また商品はいつまでにどこに納品されるのかといった情報が、
関連部署のみならず、お客様や協力会社様にもすべて共有されるかたちに。
関連資材・商品はすべてバーコード管理のため、トレーサビリティ(追跡可能性)が徹底されており、
万が一お客様に納品した商品に不具合があれば、
その商品の納品日時だけでなく、いつ納品された資材を使用したか、どの生産ラインで作られ、
生産や配送に誰が関わっていたのかといった詳細情報まで追求できるようになっています。
その他にも、納品された資材が正しいものかを調べる包材チェック、
商品出荷時のエラー判定といった、受注―生産―納品の全工程に必要な機能すべてが搭載されています。
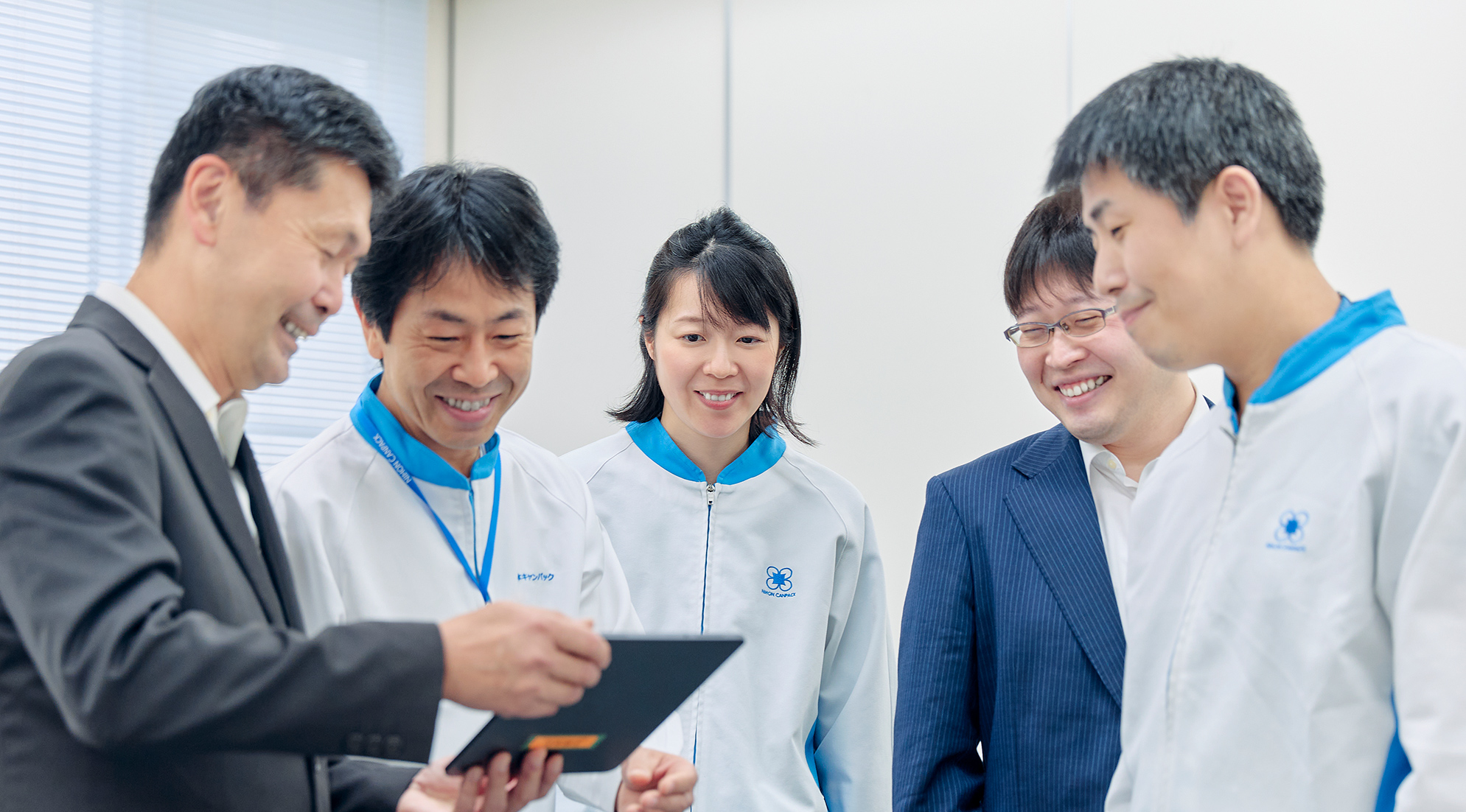
特許取得やAIの導入も実現。
常に時代の最先端をいく
開発面以外にも注力していることがあります。
PSPシステム開発を行うなかで、社内システムでありながらも関連特許を9つ取得しました。特許を取得することで、開発企業としての権利を守り、必要に応じて外部に正当な形でサービスを付与することができます。 単にシステムを作る「攻め」のみならず、資産を守る「守り」の対応も大切にしています。
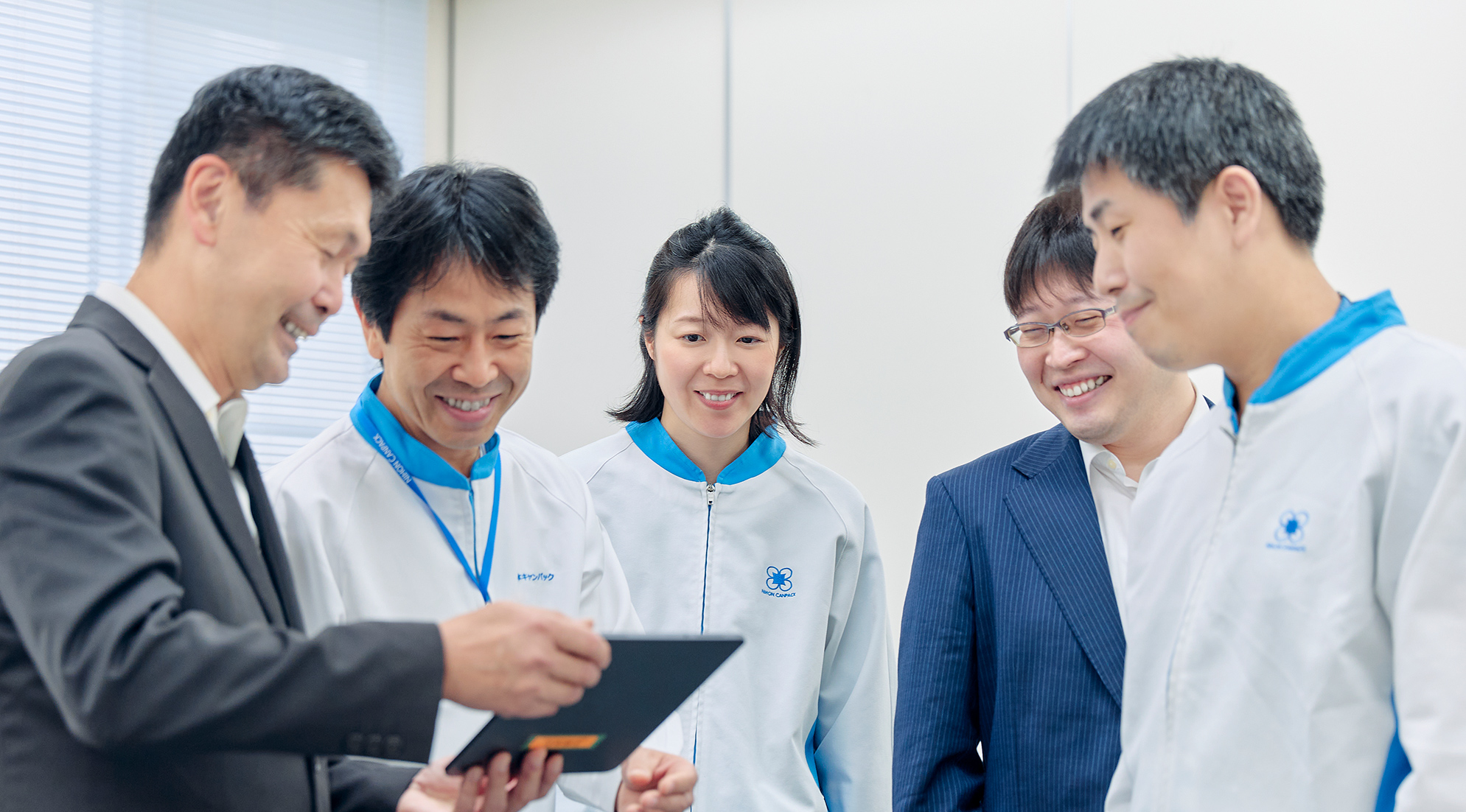
PSPシステムは現場に導入され日々活用されていますが、これで終わりではありません。
現在は、AIなどを活用した業務システムなども機能拡張に取り組むことで、
常に改善点を模索し、最先端をいくシステムを作る。このサイクルを繰り返すことで、
従業員のみならず、お客様、また協力会社様などすべての関係者にとって、
ベストなPSPシステムを実現し、より効率よく、より質の高い商品を、
これからも生産してまいります。